Artykuł sponsorowany
Dlaczego prawidłowe nakładanie teflonu jest tak ważne?
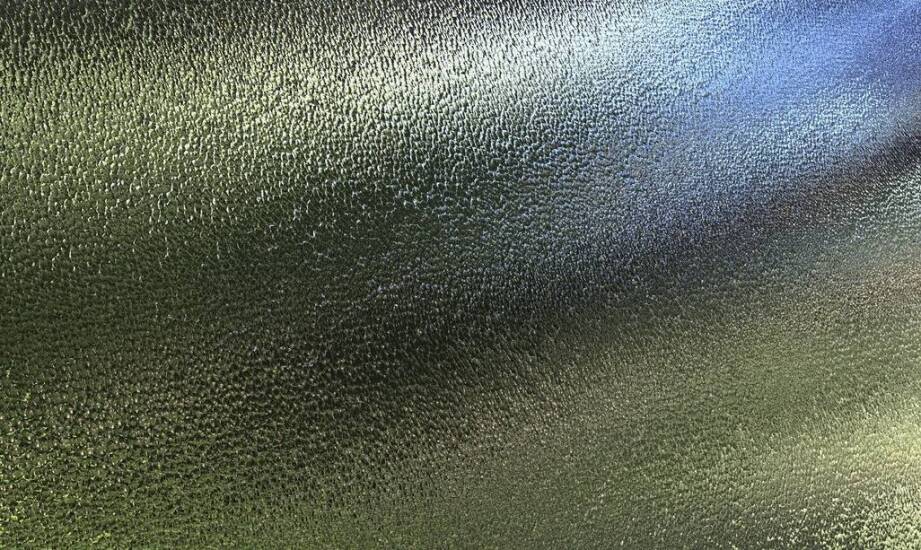
Teflon, znany również jako politetrafluoroetylen (PTFE), to materiał o wyjątkowych właściwościach, który od lat znajduje szerokie zastosowanie w różnych gałęziach przemysłu. Jego odporność na wysokie temperatury, niski współczynnik tarcia oraz doskonałe właściwości antyprzywierające sprawiają, że jest on niezastąpiony w wielu dziedzinach. Jednak aby w pełni wykorzystać te cechy, konieczne jest prawidłowe nałożenie powłoki teflonowej na dane przedmioty. W tym artykule przyjrzymy się czterem kluczowym aspektom tego procesu.
Właściwe przygotowanie powierzchni
Przed nałożeniem powłoki teflonowej, powierzchnia przedmiotu musi być odpowiednio przygotowana. Obejmuje to usunięcie wszelkich zanieczyszczeń, takich jak oleje, tłuszcze czy rdza, które mogą wpłynąć na przyczepność powłoki. Następnie powierzchnia jest szorstkowana, co zwiększa jej chropowatość i poprawia przyczepność teflonu. W zależności od rodzaju materiału i wymagań aplikacji może to obejmować piaskowanie, obróbkę mechaniczną lub chemiczną.
Wybór odpowiedniej metody aplikacji
Istnieje kilka metod nakładania teflonu, a wybór odpowiedniej zależy od rodzaju przedmiotu oraz oczekiwanych właściwości końcowego produktu. Do najpopularniejszych metod należą natrysk elektrostatyczny, malowanie pędzlem lub wałkiem oraz zanurzenie. Natrysk elektrostatyczny pozwala na równomierne pokrycie powierzchni, nawet w trudno dostępnych miejscach, podczas gdy malowanie pędzlem lub wałkiem jest bardziej odpowiednie dla prostszych kształtów. Zanurzenie stosuje się głównie w przypadku małych przedmiotów, które można łatwo zanurzyć w płynnej kompozycji teflonowej.
Kontrola jakości i grubości powłoki
Aby zapewnić optymalne właściwości powłoki teflonowej, ważne jest kontrolowanie jej jakości i grubości. Zbyt cienka warstwa może nie zapewnić wystarczającej ochrony przed zużyciem czy korozją, podczas gdy zbyt gruba może prowadzić do pęcherzy czy spękań. W związku z tym stosuje się różne techniki pomiaru grubości powłoki, takie jak mikrometry czy ultradźwiękowe mierniki grubości. Dodatkowo kontroluje się również jednorodność i przyczepność powłoki, aby wyeliminować ewentualne defekty.
Kategorie artykułów
Polecane artykuły
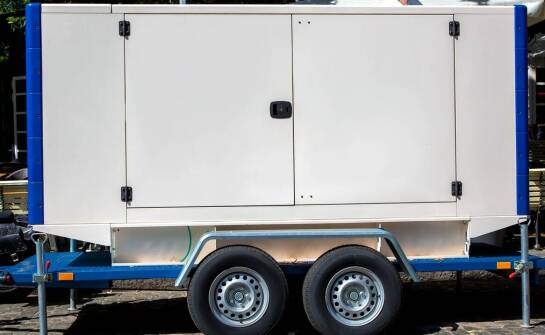
Jakie są koszty związane z wynajmem agregatów prądotwórczych?
Agregaty prądotwórcze to niezbędne urządzenia w przypadku awarii sieci energetycznej, prac budowlanych czy organizacji imprez masowych. Wiele firm decyduje się na wynajem takich urządzeń, gdyż jest to rozwiązanie bardziej ekonomiczne niż zakup własnego agregatu. Jednak jakie są koszty związane z wyn
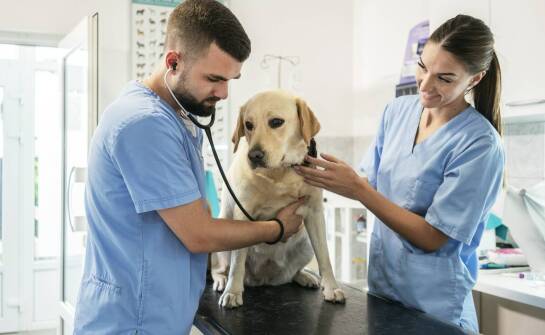
Czy istnieją rasy psów i kotów bardziej narażone na rozwój nadczynności tarczycy?
Nadczynność tarczycy to poważne schorzenie, które może dotknąć zarówno ludzi, jak i zwierzęta. W przypadku naszych czworonożnych przyjaciół, takich jak psy i koty, choroba ta może prowadzić do wielu niekorzystnych skutków zdrowotnych, takich jak zmiany w zachowaniu, osłabienie mięśni czy problemy z